El próximo mes de septiembre se cumplirá un año de la puesta en marcha del Centro de Excelencia del Sector Naval (CESENA) de Siemens en Ferrol, concretamente ubicada en el Centro de Innovación y Servicios (CIS) de A Cabana. Un proyecto que desembarcó en la comarca de la mano de Navantia y ligado al desarrollo del programa de fragatas F-110 y a la transformación digital del astillero.
En 2018, tras una visita de los responsables de Navantia al centro de referencia que Siemens tiene en Newport News, en el estado de Virginia, el astillero público solicitó a la multinacional alemana la construcción de unas instalaciones similares próximas a un astillero español. Y fue Ferrol la sede elegida. Una decisión llamada a cambiar el futuro de la industria naval en el país y especialmente en la comarca, pero que aún es, en parte, desconocida para la gran parte de la ciudadanía.
¿Qué es lo que se gesta exactamente en estas instalaciones? Juan Oliveira, responsable de Transformación Digital para el Sector Naval de Siemens Digital Industries Software, explica que «la razón de existir del centro está basada en el proceso de transformación digital que está llevando a cabo Navantia». Esto se realiza mediante tres vías. «La primera es la colaboración y ahí estamos dando soporte al programa de transformación digital de Navantia, ligado a la construcción de las F-110 y su paso a un astillero 5.0. A través del programa Elcano, donde trabajan unas 40 o 50 personas».
Por otro lado, el CESENA es uno de los socios tractores del PERTE Naval, junto con Navantia y con PYMAR. «Nuestro papel como tecnólogo es mostrar las posibilidades que las tecnologías tienen en este proceso de transformación digital del sector».
La segunda pata del centro es la de dar soporte a la innovación, no solo a los astilleros de Navantia, también a todo el ecosistema que existe alrededor: ingeniería, suministradores… «Hacemos una labor de consultoría para dar a conocer estos caminos de la innovación digital», explica Oliveira. Y la última de las patas son las personas. En este sentido, Siemens ha desarrollado un programa formativo que se llama ‘Marine Digital Twin’.
La idea de este programa es formar y certificar a trabajadores en activo del sector naval para que se pongan al día con las soluciones más punteras. «Y al mismo tiempo colaboramos con las principales universidades de España en las que se cursa formación naval. En este caso, en Ferrol, Siemens tiene un acuerdo formativo con el campus industrial de la UDC, que es el primero especializado en este campo. «También trabajamos con el campus de Cartagena, la Universidad de Cadiz y la Complutense de Madrid. Lo que hacemos es dotar a sus alumnos de todos nuestros softwares para que puedan formarse y se incorporen al mercado laboral con pleno conocimiento de estas herramientas».
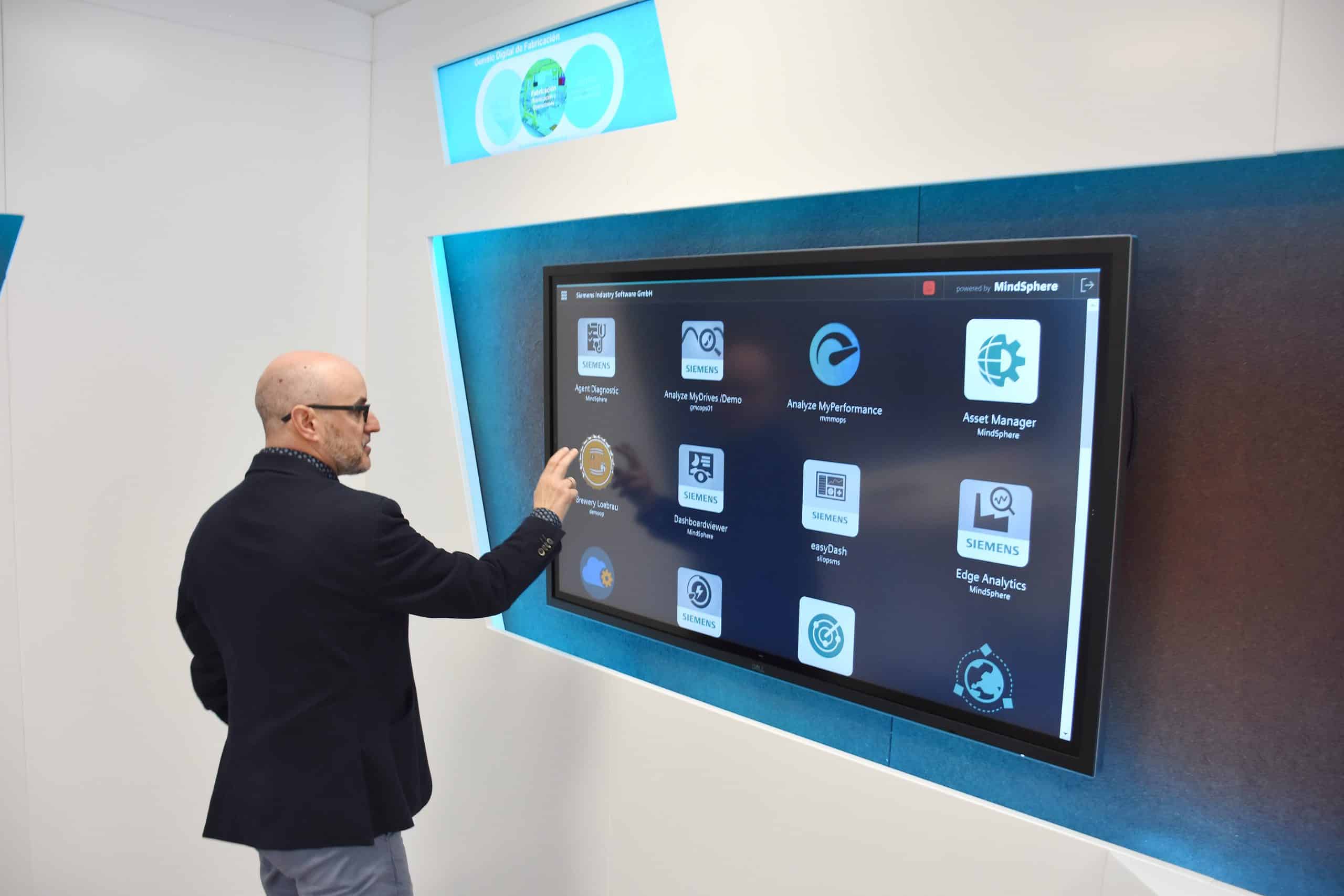
Para Juan Oliveira, que presume entre risas de ser «un ferrolano de toda la vida», la decisión de Siemens de traer a la ciudad un proyecto como este y contar, además, con personas de la zona, supone «una oportunidad única y enorme para toda la comarca». «Esto tiene que servir como impulso para que otras empresas vengan y se instalen en Ferrol y los municipios de alrededor. Y, también -apunta Juan Oliveira- debería de hacernos ser conscientes del talento que tenemos aquí y ponernos más en valor».
Recuerda que hay cinco polos de referencia para Siemens mundo: Estados Unidos (Virginia), Alemania (Hamburgo), UK, China y Ferrol. «Nuestra idea es ayudar todo lo que podamos a la Universidad. Estamos poniendo a disposición de los alumnos todas nuestras soluciones y herramientas de software, que además de un valor monetario enorme, suponen un valor añadido a su formación que hasta ahora no existía».
Asegura Oliveira que el perfil de los nuevos ingenieros va a cambiar mucho en los próximos años. La tecnología en general, pero especialmente en este sector, avanza a un ritmo en el que cuesta mucho mantenerse al día. «Estamos continuamente reciclándonos y formándonos para no quedarnos atrás. Esa es la idea de esa formación. Tener a trabajadores totalmente actualizados en las últimas innovaciones».
El centro de Siemens proporciona dos tipos de formación: una presencial, con un aula en el CESENA de Ferrol y otra en Cádiz. Pero también se realiza información on-line. El objetivo de la compañía es formar a unas 30.000 personas en los próximos años.
Gemelo Digital
Además de la formación, que supone un elemento clave en el desarrollo industrial del sector naval, uno de los proyectos más valiosos del CESENA es el del ‘Gemelo Digital’. Un término que puede parecer, a priori, complicado de entender, pero que Juan Oliveira resumen de forma sencilla en una frase: «Es una réplica virtual de un elemento físico».
En el CESENA trabajan con tres gemelos digitales: El primero es el de ingeniería y con él lo que hacen es replicar en un espacio virtual lo que será el futuro modelo físico del buque, a través de modelado 3D y herramientas de simulación. Esa fase ya se está implementando, de facto, en el programa de las F-110.
El segundo gemelo digital es el de astillero, mediante el cual, con la réplica virtual del astillero, se busca mejorar la fabricación de los buques, por ejemplo, con una mejor planificación de los trabajos, identificando cuellos de botella en ciertos procesos o mejorando tiempos. El objetivo es construir de una manera más rápida y económica. Y el tercer gemelo digital es el de la operación. «Cuando el buque ya está construido, se conecta con el gemelo digital, es decir, con la réplica virtual, y comenzamos a obtener datos de rendimiento del mundo real para compararlos con los datos simulados del funcionamiento óptimo del buque».
«A través de esa comparación es cuando puedes mejorar la operatividad del buque. Ahí se detectan posibles fallos. Supongamos, con el ejemplo de un coche, que hay que cambiar el filtro aceite a los 30.000 kilómetros porque se ha estimado así de forma genérica. Pero no puedes saber realmente cómo está funcionando ese filtro. Sin embargo, si tú tuvieras parámetros reales de cómo está funcionando, podrías optimizarlo. Es decir, pasarías de un mantenimiento preventivo a un mantenimiento predictivo en el que ya sabes que algo no está funcionando bien o no va a funcionar bien», detalle Juan Oliveira.
Un aspecto clave, tanto en el gemelo del producto como en el de la fabricación y en el de la operación, es que esta tecnología te ayuda en la toma de decisiones. «No va a tomar la decisión por ti, pero te va a dar un escenario y unas opciones realistas para que tú elijas cuál te conviene más. Por ejemplo, en el proceso de fabricación puedes simular diferentes escenarios para saber, con datos objetivos, cómo y de qué diferentes formas se podría crear una parte del buque. Eso no es asumible en el mundo real. Tú no puedes cambiar la fisonomía de un astillero, cambiar el tamaño de una grúa de un día para otro, moverla, cambiar el tamaño de los bloques… Pero en el mundo virtual sí. Y eso te puede abrir nuevas posibilidades que te ayuden a mejorar los tiempos y los costes, por ejemplo».
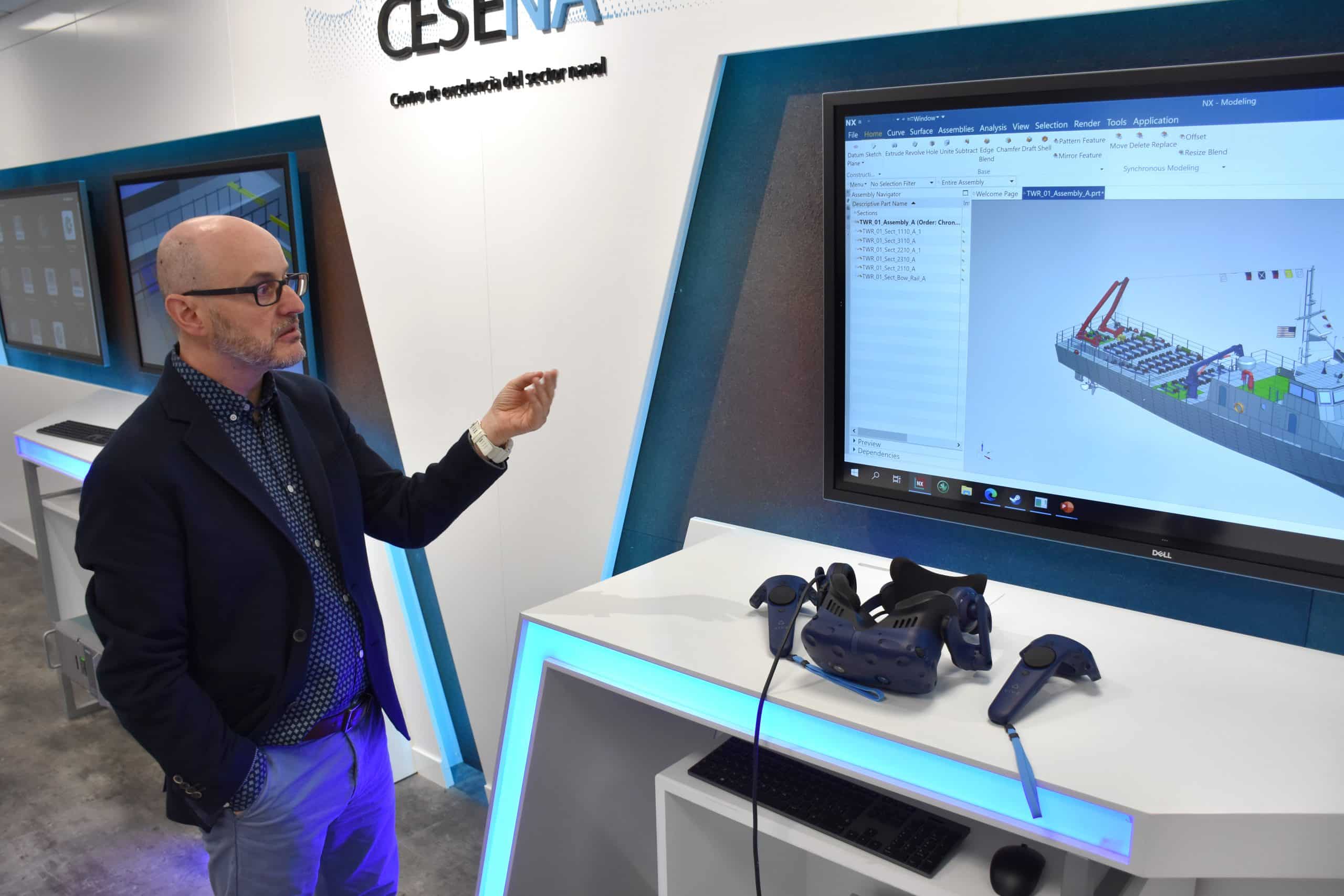
Y lo mismo ocurre en la fase de operación. Con la simulación de un gemelo digital se puede enseñar a la tripulación a manejar un buque desde tierra, sin necesidad de sacarlo al mar, con los costes que ello conlleva. Recuerda Juan Oliveira un caso real de esta aplicación: «En la Copa América de Vela el equipo Ineos probó su barco virtualmente antes de competir y detectaron algunos fallos, como zonas poco accesibles o en las que no se podían mover dos personas, otros elementos que eran difíciles de manejar en ciertas condiciones de oleaje, etc. Esto los llevó a realizar algunos cambios para adaptar el barco a esa competición y esa situación concreta».
Tiempos y costes
Como explica el ingeniero ferrolano, uno de los objetivos de este gemelo digital es el ahorro de tiempo y costes. «La tendencia del sector inevitablemente lleva a eso. A poner el tiempo y los costes en el centro de todo. Es un sector bastante volátil, que sufre mucho todo tipo de crisis, y los armadores buscan que sus beneficios se ajusten o se reduzcan lo menos posible. Por lo tanto, buscan barcos que sean más baratos de construir y más baratos de operar, pero que al mismo tiempo puedan estar el mayor tiempo posible operando»
Pero ¿cómo conseguimos esto? Pues precisamente con estas nuevas tecnologías. Mejorando los procesos de fabricación con el gemelo digital o en la propia operatividad del barco. Uno de los principales beneficios de la simulación es, precisamente, ahorrar en costes. «Podemos hacer de forma virtual todo y más de lo que podríamos hacer en el mundo real, pero sin tener que gastar tanto dinero».
Algo fundamental en un ecosistema como el sector naval, donde la competencia es feroz. «Está claro que Navantia no puede quedarse atrás en este mercado cada vez más competitivo, con el sudeste asiático empujando fuerte y rompiendo el mercado en costes. Cada vez es más difícil conseguir nuevos contratos y poder seguir entre los astilleros de referencia implica subirse al carro de la transformación digital».
Sostenibilidad
Pero el precio y el coste no son los únicos parámetros a tener en cuenta. Las normativas marítimas internacionales cada vez son más exigentes en términos de sostenibilidad y buscan reducir las emisiones de gases de efecto invernadero a niveles máximos en 2050. También aquí el gemelo digital ayuda a las compañías a cumplir con estos estándares.
«Nuestro software te probar miles de formas y pequeñas modificaciones en el casco de un buque para comprobar cuál hace que consuma lo menos posible y que eso se traduzca en muchas toneladas menos de emisiones. Y, además, eso se puede conjugar con que el buque se fabrique con el menor acero posible, por ejemplo».
Apuesta de Siemens por la transformación digital
En los últimos 17 años, la compañía alemana se ha dotado de diferentes programas informáticos para poder generar un ciclo completo de soluciones, de principio a fin. Lo que se conoce como ‘end to end’. «Esto ha sido clave para que Navantia nos eligiera. Que podamos cubrir el proceso completo de la vida de un buque de manera virtual: desde el diseño inicial o la simulación, hasta la fase final de servicio y mantenimiento», asegura Oliveira.
Hace justo un año, poco después de poner en marcha la oficina de Ferrol, Siemens adquirió FORAN, un software de referencia en ingeniería naval, lo que daba buena cuenta de la apuesta de la empresa por este sector. Además, en los últimos diez años la empresa ha invertido más de 10.000 millones en la adquisición de empresas y productos de este tipo, que han permitido a Siemens posicionarse como líder mundial en la gestión y desarrollo de estas herramientas.